无人纯电动物流车驱动桥设计(含CAD图,CATIA三维图)英文版
无需注册登录,支付后按照提示操作即可获取该资料.
无人纯电动物流车驱动桥设计(含CAD图,CATIA三维图)英文版(任务书,开题报告,文献摘要,论文说明书英文8000字,CAD图8张,CATIA三维图)
Design of drive axle for unmanned pure electric logistics vehicle
Abstract
With the increasing awareness of energy crisis and environmental protection, people pay more attention to pure electric vehicles. Some potential traditional automobile manufacturers at home and abroad often position their products in a high level, so it is difficult to popularize them among majority consumers. As a supplement to middle and high level pure electric vehicles, small and micro pure electric vehicles will reveal a great development potential. This kind of pure electric vehicle has the advantages of compact structure, light weight and low cost.
In this paper, the driving axle of an unmanned electric logistics vehicle based on XinShiQi Company is designed with the help of three-dimensional modeling software CATIA, and finite element analysis software ANSYS. In the design, the characteristics of the drive axle are explained firstly. According to the given data, the structure types and parameters of the final drive, differential, half shaft and universal joint are determined, and the strength is checked. Through calculating the size and referring to the similar parts of the existing vehicle, carry out the 3D model. Then import the model into finite element analysis software to obtain stress nephogram. The results are of great significance to the design and development of the driving axle of the electric logistics vehicle.
Key words: drive axle; electric logistics vehicle; final drive; differential
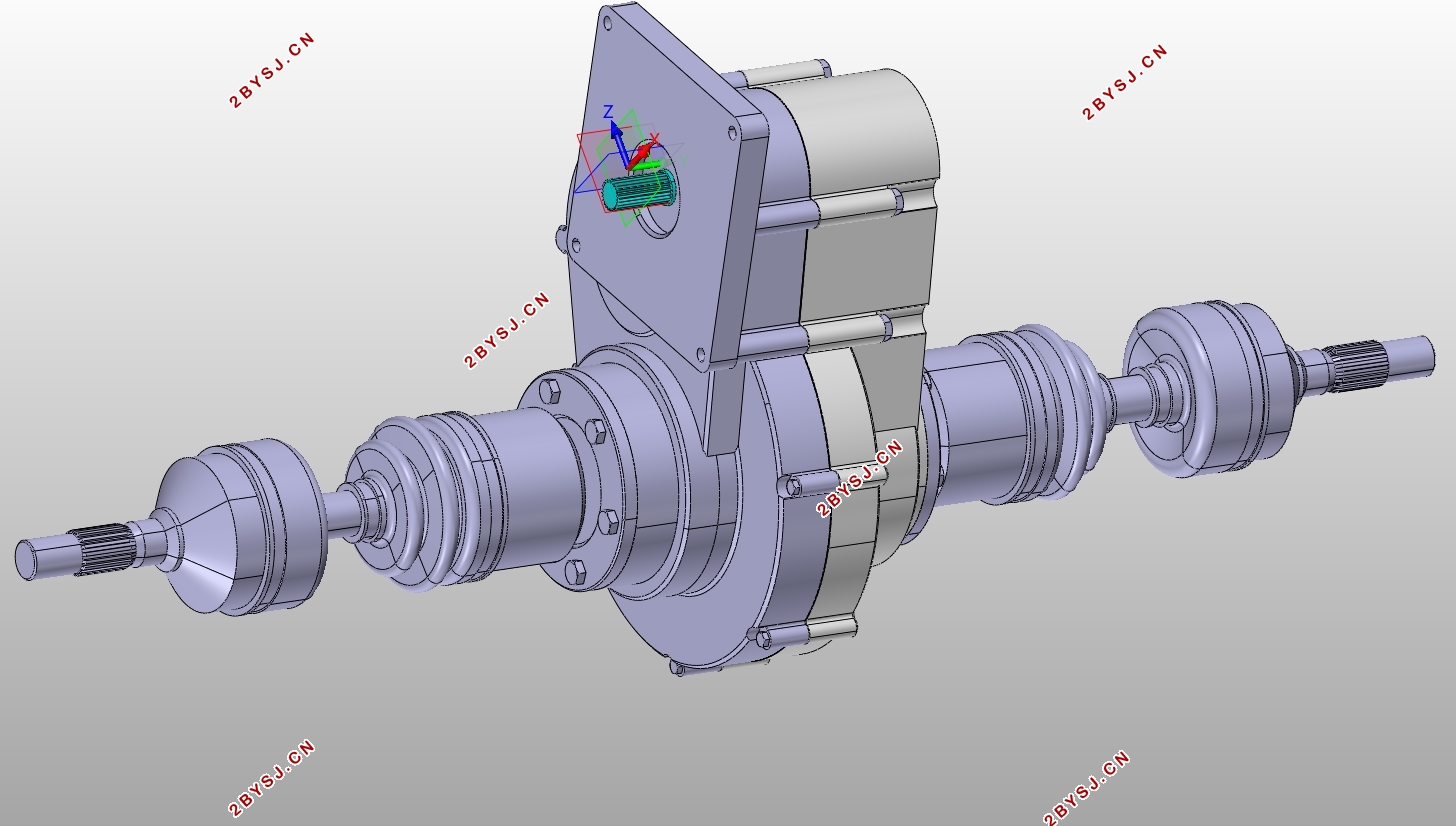



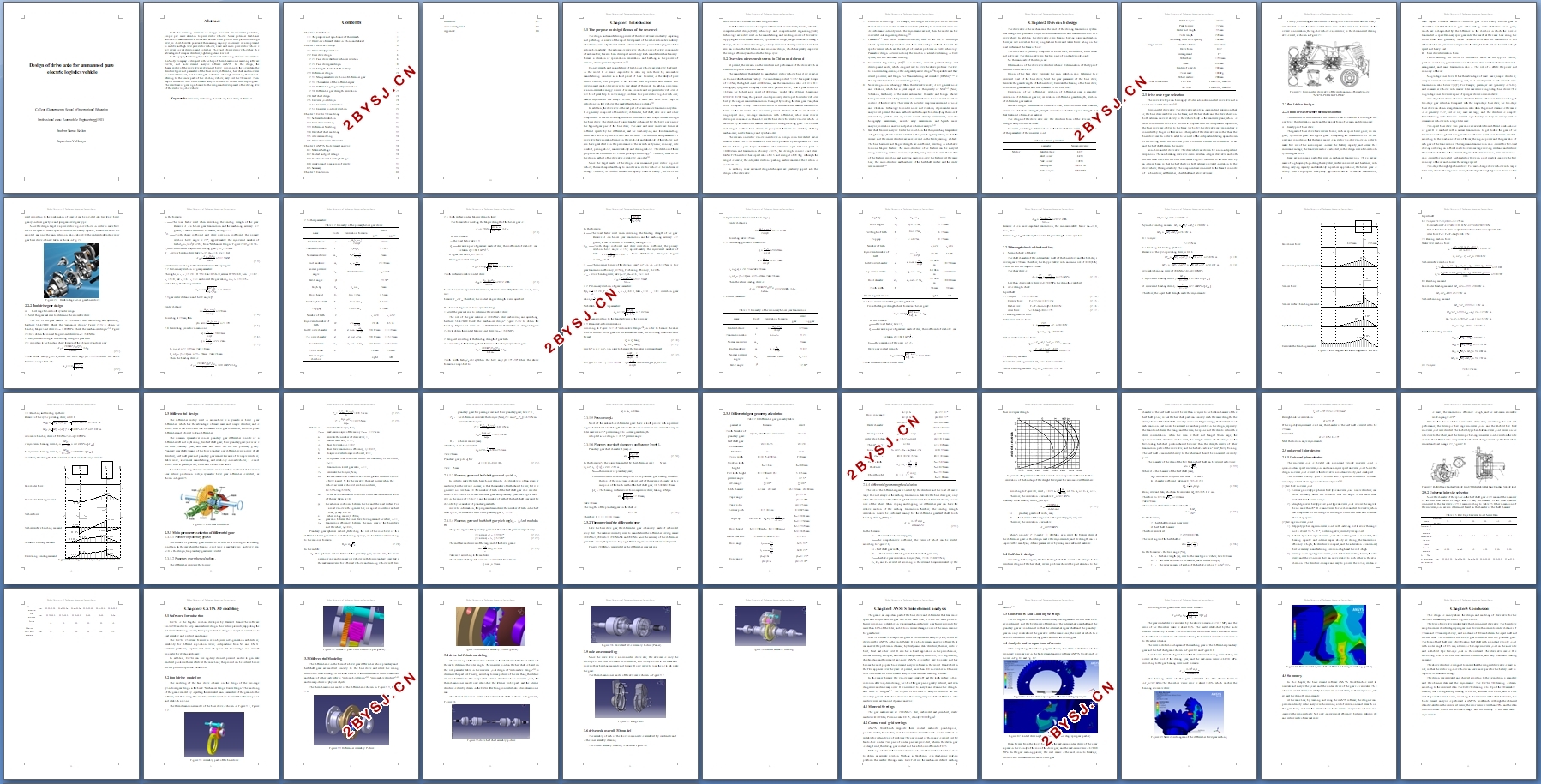
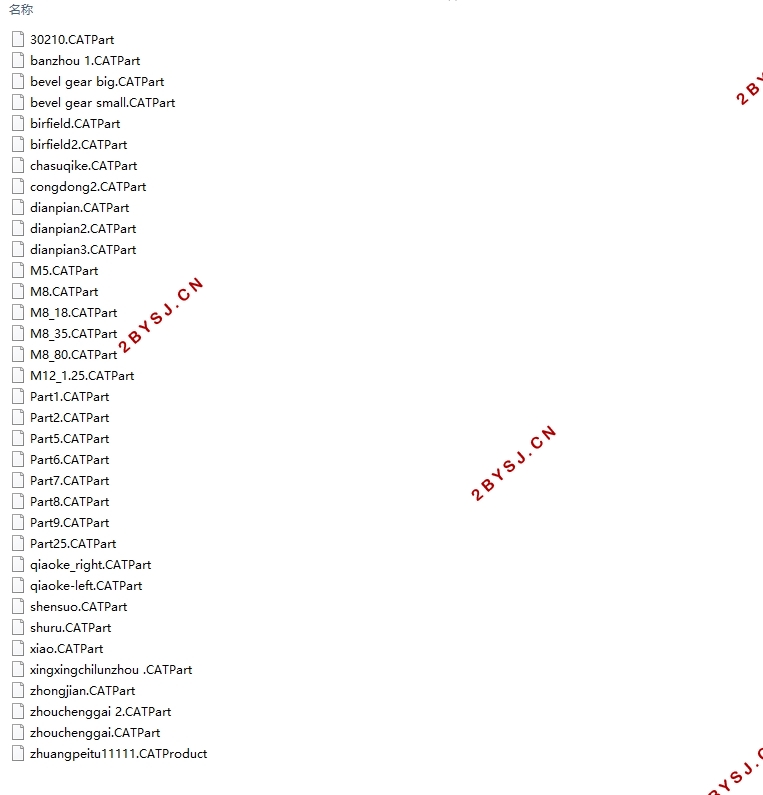

Contents
Chapter 1 Introduction 1
1.1 The purpose and significance of the research 1
1.2 Overview of research status in China and abroad 2
Chapter 2 Drive axle design 4
2.1 Drive axle type selection 5
2.2 Final drive design 6
2.2.1 Final drive structure technical solution 6
2.2.2 Final drive gear design 8
2.2.3 Strength check of shaft and key 15
2.3 Differential design 20
2.3.1 Main parameters selection of differential gear 20
2.3.2 The material of the differential gear 23
2.3.3 Differential gear geometry calculation 24
2.3.4 Differential gear strength calculation 25
2.4 Half shaft design 26
2.5 Universal joint design 28
2.5.1 Universal joint selection 28
2.5.2 Universal joint size selection 29
Chapter 3 CATIA 3D modeling 31
3.1 Software Introduction 31
3.2 Final drive modeling 31
3.3 Differential Modeling 32
3.4 Drive half shaft modeling 33
3.5 Axle case modeling 34
3.6 Drive axle overall 3D model 34
Chapter 4 ANSYS finite element analysis 36
4.1 Material Settings 36
4.2 Contact and grid settings 36
4.3 Constraints And Loading Settings 37
4.4 Analysis and comparison of results 37
4.5 Summary 39
Chapter 5 Conclusion 40
References 41
Acknowledgement 43
Appendix 44