HTD16塑料斜齿轮注射成型工艺分析与模具设计(含CAD图,UG三维图)
无需注册登录,支付后按照提示操作即可获取该资料.
HTD16塑料斜齿轮注射成型工艺分析与模具设计(含CAD图,UG三维图)(任务书,开题报告,论文说明书13000字,CAD图5张,UG三维图)
摘要
本文以POM塑料斜齿轮为对象,对其进行注射成型工艺分析以及注塑模具的设计。从材料的选择出发,进行了斜齿轮结构的设计,分析了其结构工艺性和注塑成型的工艺性,阐明了注塑机的选择、分型面的确定、浇注系统及凝料推出机构、成型零件、脱模机构、定距分型机构、温度调节系统等详细的设计过程。其中实现斜齿轮成功脱模的旋转脱模机构是整个设计的重要部分,它通过在推管上开设螺旋槽,并在型芯上插入导向销的方式使推管在向上推出塑件的同时发生旋转,以此带动塑件旋转,从而使塑件沿着齿型型腔顺利旋转脱出。同时在定距分型机构设计方面,由于普通的分型机构无法满足分型面打开的要求,故自己设计一简易弹开机构来保证分型面的顺序分离。
关键词: 斜齿轮;注塑模;一模四腔;旋转脱模
Abstract
This paper carrying on the injection molding process analysis and a four-cavity injection mold design is targeted at the plastic helical gear.Starting from the selection of the material,this paper carrys out the design of the helical gear structure and analyzes the processability of the structure,it also elaborates the detailed design process of the selection of the injection molding machine, the determination of the parting surface, the feed system and the launch agencyof thecondensate, the forming parts, stripping mechanism, fixed distance classification mechanism and the temperature control system. The successful stripping mechanism of the helical gear is an important part of the whole design which opens the spiral groove on the ejector sleeve and inserts the guide pin on the core so that the ejector sleeve rotates while pushing out the plastic parts,leading to the plastic parts rotate along the teeth type cavity smoothly out. At the same time, in the design of the fixed pitch classification mechanism ,due to the general classification mechanism can not meet the requirements of sub-surface open, so I design a simple bounce mechanism to ensure the separation of the sub-surface.
Key Words:helical gear; injection mold;four-cavity;rotation stripping
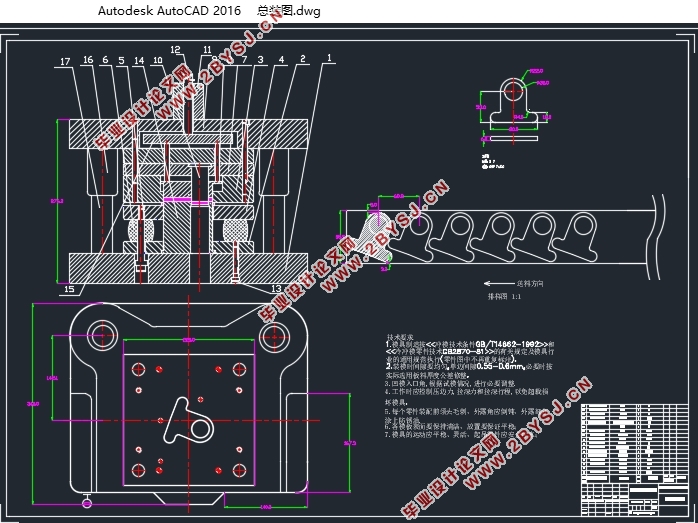
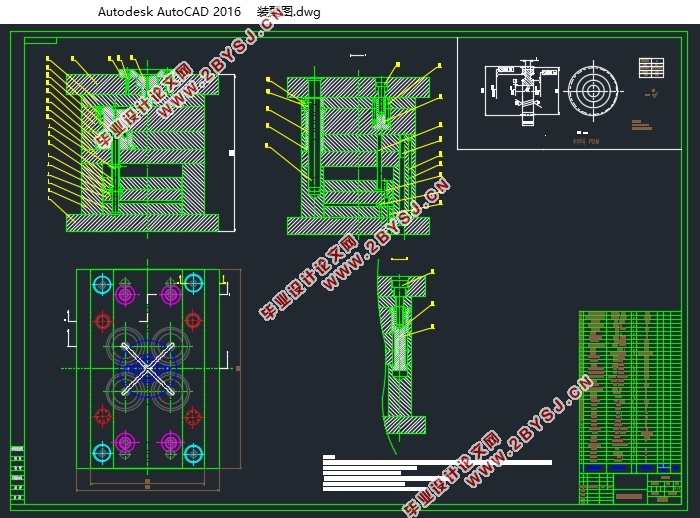
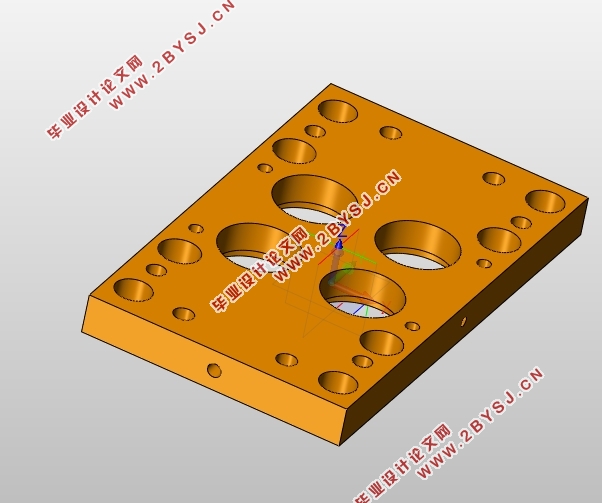
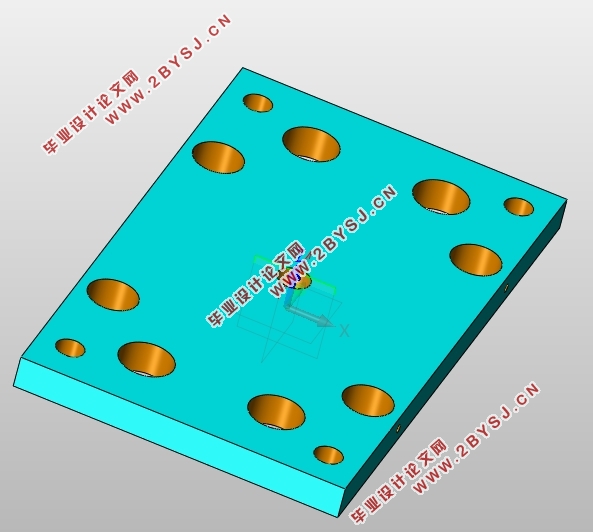
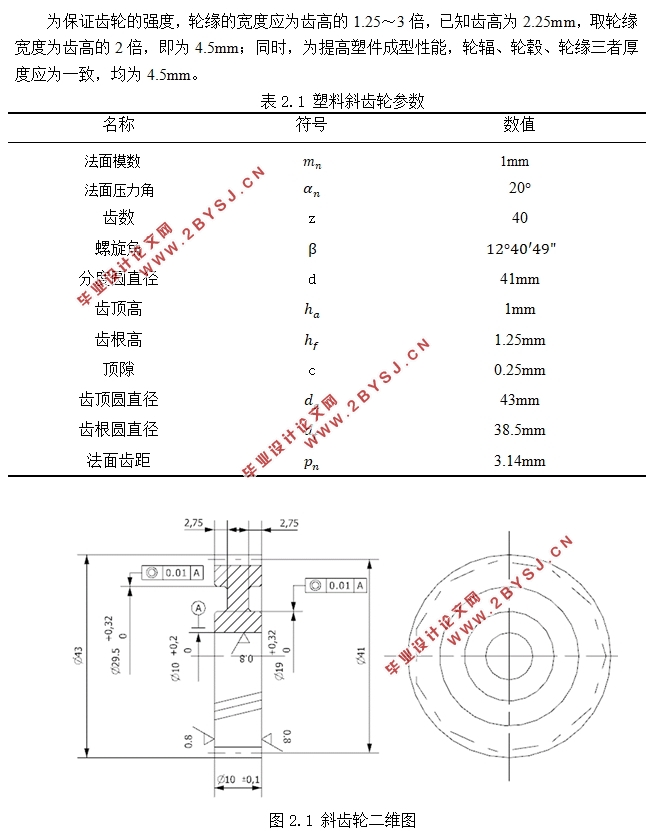
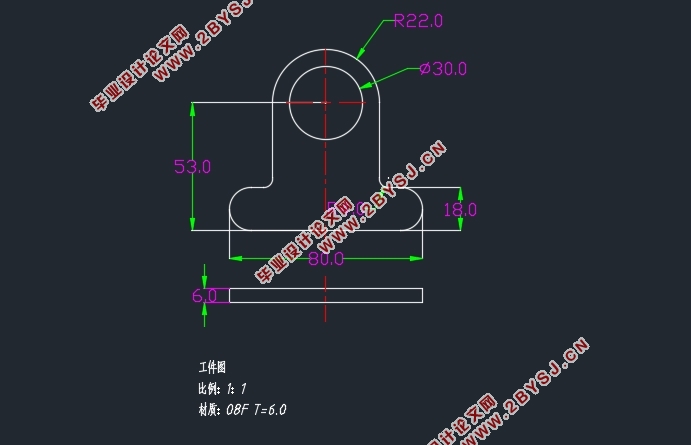
目录
第1章绪论 1
1.1 塑料斜齿轮注射成型技术发展现状 1
1.2 塑料斜齿轮注射成型技术发展趋势 1
1.3 塑料斜齿轮注塑模设计的目的及意义 2
第2章塑料斜齿轮的设计 4
2.1 斜齿轮材料的选择 4
2.2 斜齿轮结构设计 4
第3章斜齿轮塑件的工艺性分析 6
3.1 斜齿轮结构工艺的分析 6
3.2 POM成型性能分析 6
3.3 POM成型条件 7
3.4 斜齿轮注塑成型工艺分析 7
第4章注塑机的选择及校核 9
4.1 注塑机的选择及参数 9
4.2 注塑机的校核 10
第5章模具结构设计 11
5.1 分型面的选择 11
5.2 浇注系统设计 11
5.2.1 浇注系统的布置 11
5.2.2 主流道设计 12
5.2.3 浇口套的设计 13
5.2.4 定位圈设计 13
5.2.5 分流道设计 13
5.2.6 浇口设计 13
5.2.7 冷料穴设计 14
5.2.8 阻料沟的设计 14
5.2.9 流道剪切速率的校核 15
5.3 脱模机构设计 15
5.3.1 脱模力的来源 15
5.3.2 脱模力的计算 16
5.3.3 推出机构的确定 17
5.3.4 推出力的校核 17
5.3.5 顺序脱模机构 18
5.4成型零件的设计 19
5.4.1 成型零件的结构设计 19
5.4.2 成型零件工作尺寸计算 20
5.4.3 壁厚计算 21
5.5 结构零部件设计 22
5.6 导向定位系统设计 23
5.6.1 导向系统设计 23
5.6.2 定位系统设计 23
5.7 温度调节系统设计 24
5.7.1 热平衡计算 24
5.7.2 加热系统设计 26
第6章结论 27
参考文献 29
致谢 31