插座上壳注塑模具的设计(Moldflow模流分析)
无需注册登录,支付后按照提示操作即可获取该资料.
插座上壳注塑模具的设计(Moldflow模流分析)(论文说明书18000字,Moldflow模流分析)
摘要:塑料工业是当今世界上增长最快的工业门类之一,而注塑模具是其中发展较快的种类。因此,研究注塑模具对了解塑料产品的生产过程和提高产品质量有很大意义。本设计介绍了插座上壳注射成型的基本过程,对注塑产品提出了基本的设计原则;详细介绍了塑件成型工艺设计,注射机的选择,浇注系统的的设计,成型零件的结构设计,脱模推出机构的设计,冷却系统的设计的过程。并对标准模架的选择也作了相应的介绍。通过本次设计,使我掌握了注塑模具设计的全过程,同时也提高了运用CAD绘制复杂装配图的能力。
关键词:塑料;注塑模具;模具结构
尺寸和精度
由于该塑件是方体形状,而且是做外面的盖,所以尺寸和精度要求不是很高,所以经分析选择一般精度等级13级精度。
该塑件形状很规则轮廓,分模方向容易认出,容易模塑,所以采用单分型面,而且该塑件厚度小,易脱模。
工件的臂厚
工件的壁厚对塑件的质量影响很大,壁厚过小,成型时流动阻力大,大型复杂制品就难以充满型腔,壁厚过大,不但造成原料的浪费,而且对热固性材料成型来说增加了压塑的时间,而且容易造成固化不完全,对热塑性材料来说就回增加冷却时间,所以初步估计为该塑件壁厚为4mm。
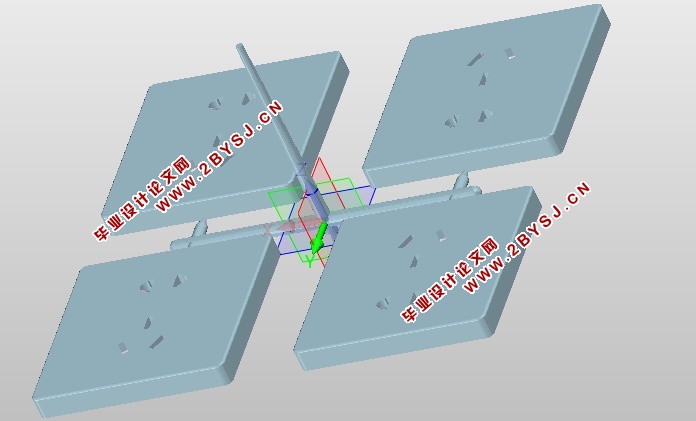
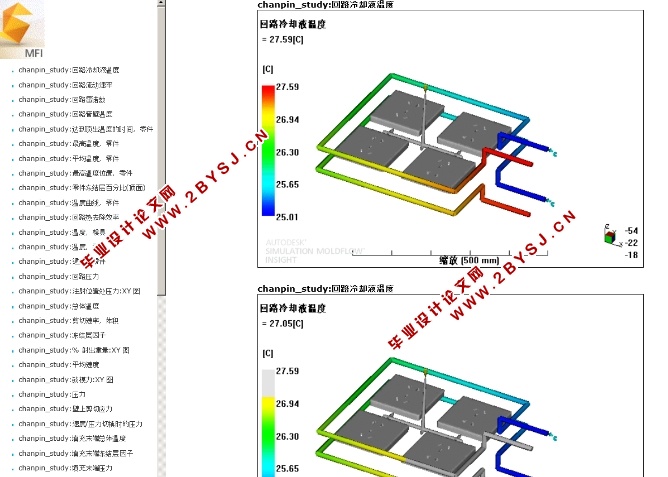
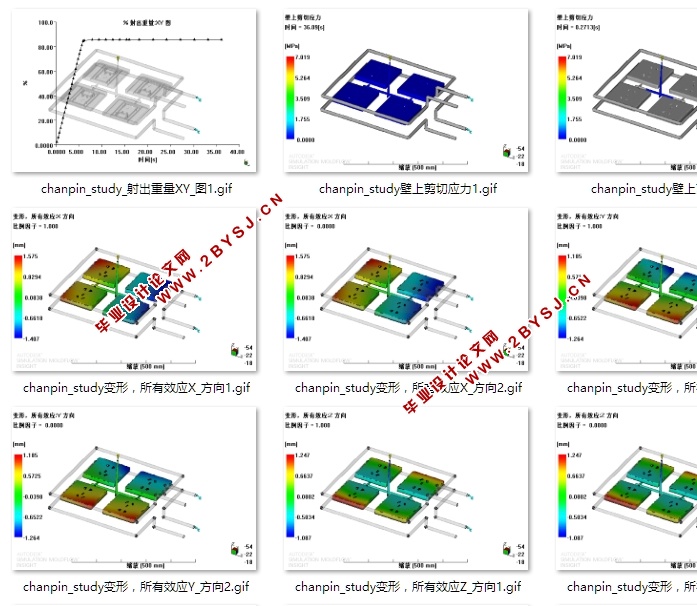

目录
插座上壳注塑模具的设计 2
Outlet shell injection mould design 3
第一章 绪论 1
1.1 塑料模具设计的重要性 1
1.2 塑料模具的分类 1
1.2.1 塑料注射(塑)模具 1
1.2.2 塑料压塑模具 2
1.2.3 塑料挤出模具 2
1.2.4 塑料吹塑模具 3
1.2.5 吸塑模具 3
1.2.6 发泡聚苯乙烯成型模具 3
1.3 我国模具的发展现况 5
第二章 工艺方案及分析 7
2.1 设计塑件时必须考虑的几个方面的问题 7
2.2 尺寸和精度 7
2.3 工件的形状及尺寸 7
2.4 工件的臂厚 9
2.5工件材料 9
2.5.1 工件材料的选择 9
2.5.2 工件材料性能分析 9
第三章 模具结构形式的拟定 11
3.1 确定型腔数量及其排列方式 11
3.2 模具结构形式的确定 12
第四章 工件的体积估算和注射机型号的选择 13
4.1 估算零件体积和投影面积。 13
4.2 锁模力 13
4.4 注塑机的校核 14
第五章 浇注系统的设计 17
5.1 主流道的设计 17
5.2 冷料井和拉料杆的设计 18
5.3 分流道的设计 19
5.4 浇口的设计 20
第六章 成型零部件的设计 22
6.1 分型面的确立 22
6.2 排气槽的设计 24
6.3 成型零件的结构设计 24
6.3.1 型腔的结构设计 24
6.3.2 型芯的结构设计 24
6.3.3 成型零件的尺寸计算 24
第七章 合模导向机构的设计 27
7.1 导柱的设计 27
7.2 导套的设计 27
第八章 塑件脱模机构的设计 29
8.1 推出机构的设计 29
8.2 复位的设计 30
8.3 脱模过程 30
8.4 模架的设计 30
第九章 冷却系统的设计 32
9.1 冷却管道的影响 32
9.2 冷却时间的计算 32
9.3 冷却道开设原则 33
9.4冷却水道的结构 33
第十章 模具的装配 35
10.1 组件型腔和型芯与模板的装配 35
10.2 推杆的装配要求 35
10.3 模具总装配程序 36
10.4 该模具的装配要求 37
10.5 模具的装配工艺 37
第十一章 moldflow分析及应用 39
11.1 Moldflow软件简介 39
11.2 插板上盖实体及其材料分析 40
11.2.1分子结构 40
11.2.2 ABS主要特性 41
11.3 插板上盖成型条件及设定 41
11.4 ABS成型参考工艺表 42
第十二章 插板上盖的模拟成型分析 44
12.1 具体方案的确定 44
12.2 moldflow成型工艺设定 45
12.3 充填时间分析 47
12.4 流动前沿温度分析 48
12.5 顶出时体积收缩率 49
12.6 锁模力的分析 50
12.7 冻结层因子分析 51
12.8 熔接线分析 53
12.9 变形量分析 54
12.10冷却系统,零件冷却后温度 57
结 论 58
参 考 文 献 59
致 谢 60